'The greater the responsibility, the more I like something'
Bart Dieterman works through NextGen at Ausnutria, producer of high-quality baby and infant food. After two and a half years, it is now time to take stock: what has he learned? What has he been able to contribute to the growth of Ausnutria? And what role does NextGen play in this? We talk to Bart and his manager Nick Zeefat.
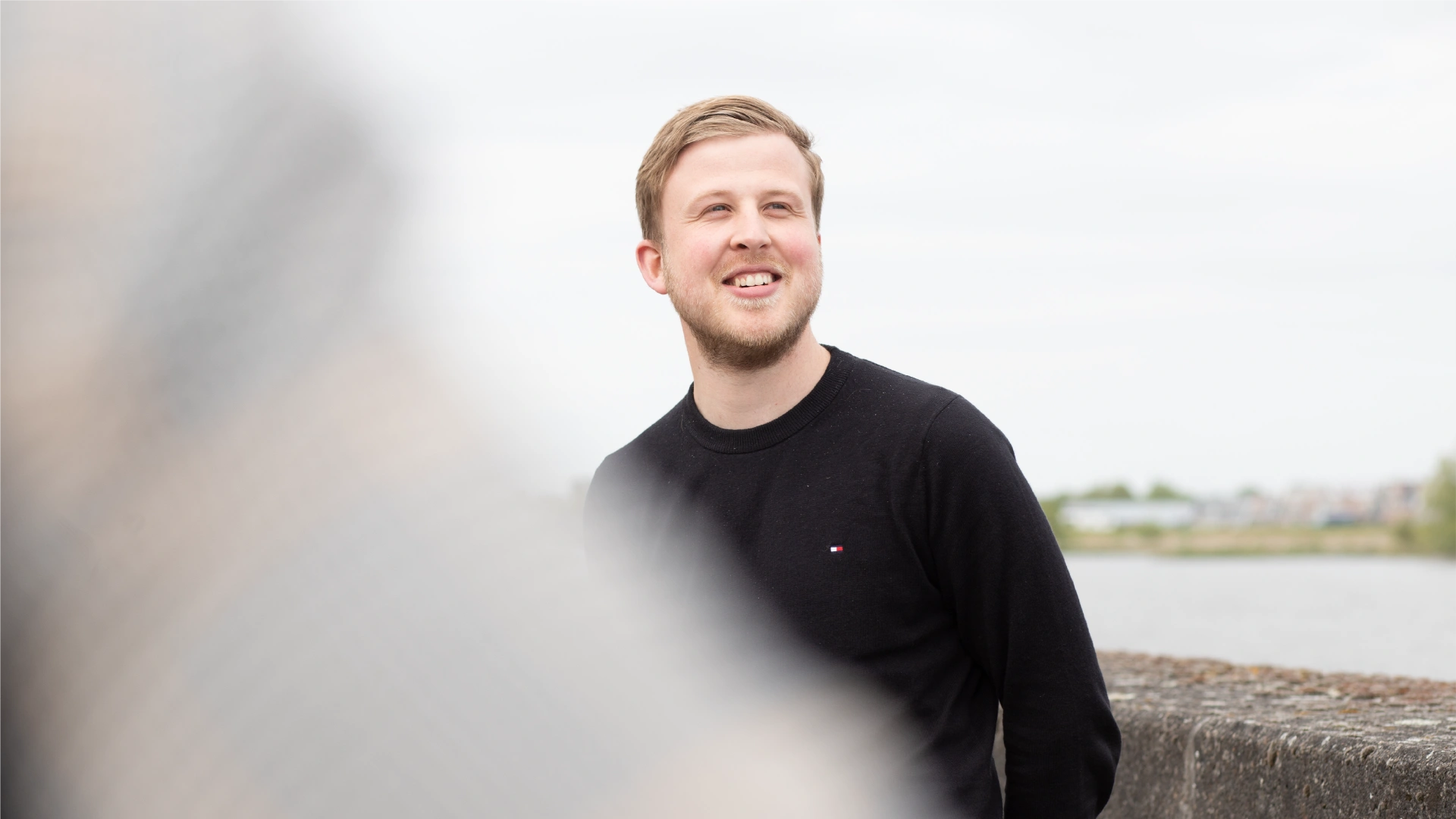
The contact was very good
Bart: During the conclusion of my studies in Technology and Operations Management and Supply Chain Management, I was approached by NextGen. That contact went very well, the role they saw for me at Ausnutria matched what I wanted and so I soon started as a production planner and manufacturing engineer, here in Kampen. Initially in a temporary position, then I stayed longer to further develop myself and Ausnutria."
Nick: In the beginning, Bart supported me in my work, but that changed over time. He does and did a lot, from monitoring and reporting production performance to initiating and supervising improvement projects.
Bart: I had quite a broad position and was involved in manufacturing, planning and energy management, among other things. I learned a lot from that, it gave me a broad view of what is involved in a production company and how we can improve processes. Ausnutria is a fast-growing company, there is a lot of development going on and that offers many opportunities to redesign processes. We are really in the process of professionalization, from young company to real corporate. I have learned an enormous amount from that.
Soft skills in practice
Nick: In this role, it is very important that you are entrepreneurial. You have to be able to figure out for yourself what is important to our organization, and how to make that clear to the decision makers. That's something that has to be kind of in you, but also something that you learn when you're in this role. And I see how NextGen helps with that.
Bart: The soft skills you learn during the NextLevel program can be put into practice immediately. You learn what personality you have yourself, what your colleagues have, and how you relate to others and can best deal with them. This has helped me a lot, especially in collaborations with management. I now understand why some individuals clash with each other and how to avoid it. It is very cool to use the theory in practice.
Nick: Bart has really learned to get others moving. If you want to get projects off the ground here, you have to be able to get people to want to work for you. In this role you are not a manager, but you do have to get people moving. That doesn't just happen; it requires experience and the ability to deal with people. He has really developed in that.
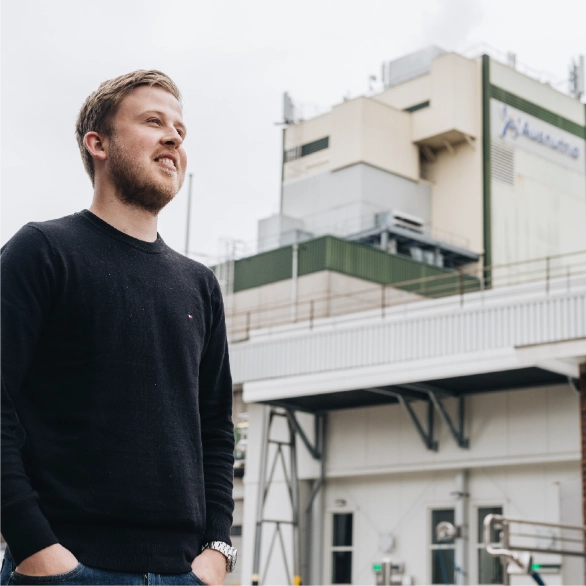
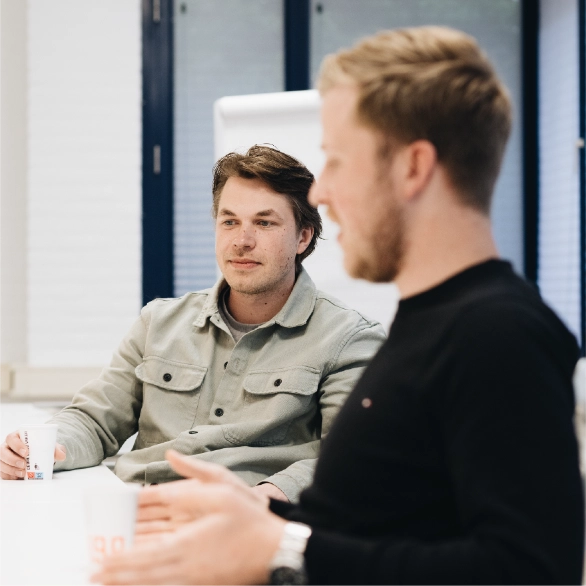
Soft skills in practice
Analyze and improve
Bart: It's also kind of in me. In this role I am analyzing current performance and spotting opportunities for improvement. I turn that into an idea, and I have to sell that idea internally. In addition, you have to be able to implement that idea yourself, with help from others, of course, but you do need them. That way of working suits me very much. If you want to change something here you are not stopped, but you have to put your own energy into it. That creates freedom and responsibility, for me that is one of the biggest advantages of working at Ausnutria. And that's also how I prefer to learn: make plans, try, learn.
Nick: I can always leave Bart very free. Of course, sometimes I ask critical questions about certain choices, but I've never had to tell him to work harder to meet certain goals or deadlines. That's the kind of people we're looking for here. Bart wants to continuously improve. If he improves personally, we also improve as a company.
Bart: A good example of this is the Green Belt training I took through NextGen, and the practical assignment that came with it. There was too little capacity here in the factory, so we made sure that the cleaning time in a production line could be significantly reduced. That was very valuable, both in terms of the learning process and in ensuring higher production together and thus higher sales. For me, this is where the value of the collaboration between NextGen, the colleagues at Ausnutria and myself really lies.
Analyze and improve
Analyze and improve
Bart: It's also kind of in me. In this role I am analyzing current performance and spotting opportunities for improvement. I turn that into an idea, and I have to sell that idea internally. In addition, you have to be able to implement that idea yourself, with help from others, of course, but you do need them. That way of working suits me very much. If you want to change something here you are not stopped, but you have to put your own energy into it. That creates freedom and responsibility, for me that is one of the biggest advantages of working at Ausnutria. And that's also how I prefer to learn: make plans, try, learn.
Nick: I can always leave Bart very free. Of course, sometimes I ask critical questions about certain choices, but I've never had to tell him to work harder to meet certain goals or deadlines. That's the kind of people we're looking for here. Bart wants to continuously improve. If he improves personally, we also improve as a company.
Bart: A good example of this is the Green Belt training I took through NextGen, and the practical assignment that came with it. There was too little capacity here in the factory, so we made sure that the cleaning time in a production line could be significantly reduced. That was very valuable, both in terms of the learning process and in ensuring higher production together and thus higher sales. For me, this is where the value of the collaboration between NextGen, the colleagues at Ausnutria and myself really lies.
Complex, high-impact projects
Nick: NextGen's guidance during projects is very valuable. Together we provide a plan and set deadlines. NextGen ensures that there are clear agreements and that a project has a head and a tail. That reduces the risk for all parties. And in addition, there is good guidance. This project was ultimately completed entirely on schedule and has yielded more than we had expected.
Bart: That also gives good, new energy. I was actually going to stop at Ausnutria, but together we decided that I will now also go for the Black Belt. In the coming months, I am going to implement the same improvement process as I did before, but one that is a lot more complex. The responsibility is greater, but so is the impact. And the more responsibility I can grab, the more I like something.
'The greater the responsibility, the more I like something'
Bart Dieterman works through NextGen at Ausnutria, producer of high-quality baby and infant food. After two and a half years, it is now time to take stock: what has he learned? What has he been able to contribute to the growth of Ausnutria? And what role does NextGen play in this? We talk to Bart and his manager Nick Zeefat.
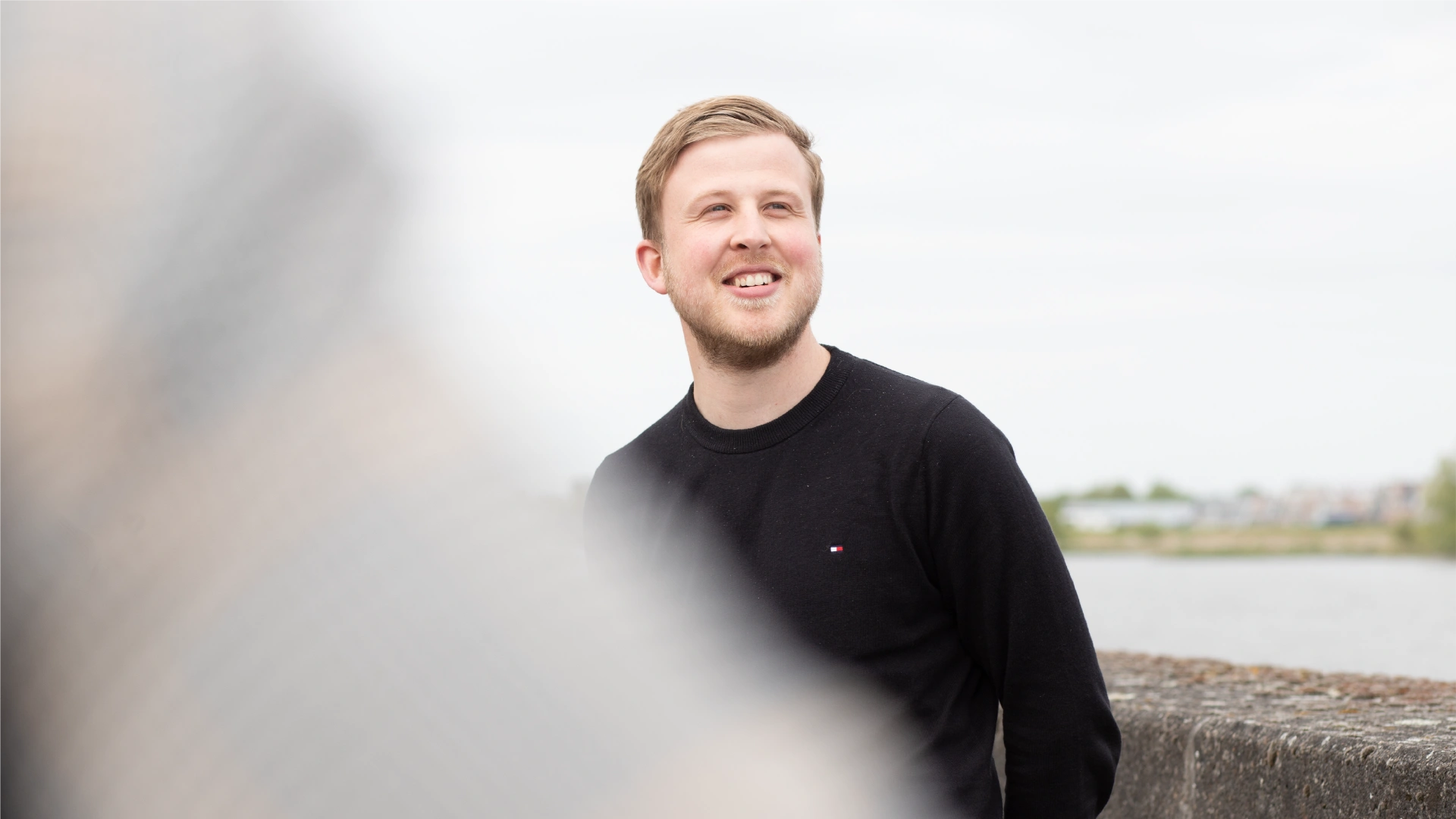
The contact was very good
Bart: During the conclusion of my studies in Technology and Operations Management and Supply Chain Management, I was approached by NextGen. That contact went very well, the role they saw for me at Ausnutria matched what I wanted and so I soon started as a production planner and manufacturing engineer, here in Kampen. Initially in a temporary position, then I stayed longer to further develop myself and Ausnutria."
The contact was very good
Bart: During the conclusion of my studies in Technology and Operations Management and Supply Chain Management, I was approached by NextGen. That contact went very well, the role they saw for me at Ausnutria matched what I wanted and so I soon started as a production planner and manufacturing engineer, here in Kampen. Initially in a temporary position, then I stayed longer to further develop myself and Ausnutria."
Nick: In the beginning, Bart supported me in my work, but that changed over time. He does and did a lot, from monitoring and reporting production performance to initiating and supervising improvement projects.
Bart: I had quite a broad position and was involved in manufacturing, planning and energy management, among other things. I learned a lot from that, it gave me a broad view of what is involved in a production company and how we can improve processes. Ausnutria is a fast-growing company, there is a lot of development going on and that offers many opportunities to redesign processes. We are really in the process of professionalization, from young company to real corporate. I have learned an enormous amount from that.
Soft skills in practice
Nick: In this role, it is very important that you are entrepreneurial. You have to be able to figure out for yourself what is important to our organization, and how to make that clear to the decision makers. That's something that has to be kind of in you, but also something that you learn when you're in this role. And I see how NextGen helps with that.
Bart: The soft skills you learn during the NextLevel program can be put into practice immediately. You learn what personality you have yourself, what your colleagues have, and how you relate to others and can best deal with them. This has helped me a lot, especially in collaborations with management. I now understand why some individuals clash with each other and how to avoid it. It is very cool to use the theory in practice.
Nick: Bart has really learned to get others moving. If you want to get projects off the ground here, you have to be able to get people to want to work for you. In this role you are not a manager, but you do have to get people moving. That doesn't just happen; it requires experience and the ability to deal with people. He has really developed in that.
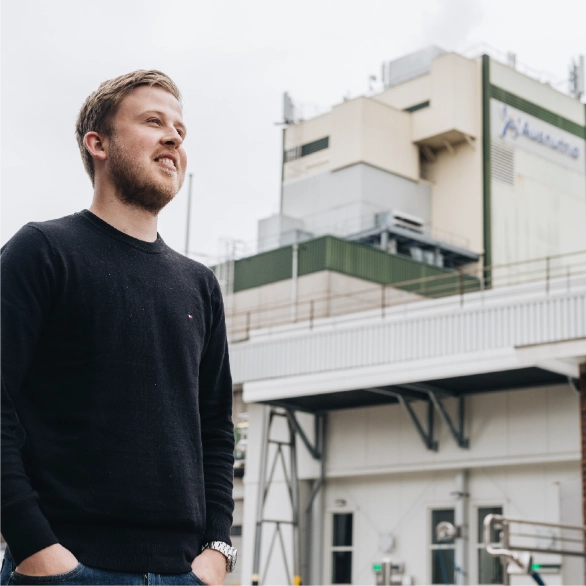
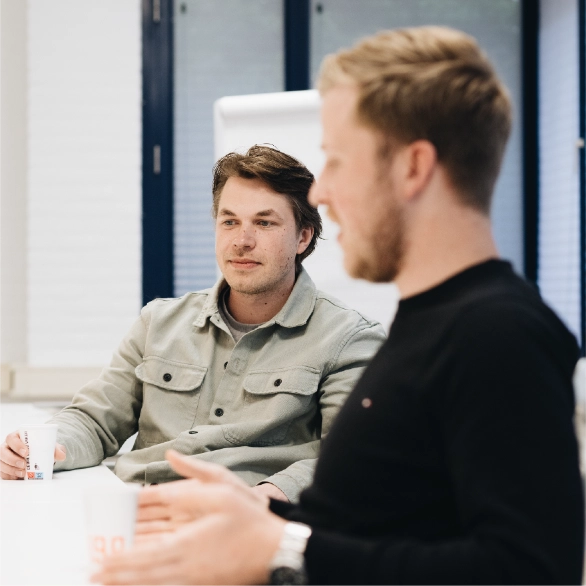
Soft skills in practice
Analyze and improve
Bart: It's also kind of in me. In this role I am analyzing current performance and spotting opportunities for improvement. I turn that into an idea, and I have to sell that idea internally. In addition, you have to be able to implement that idea yourself, with help from others, of course, but you do need them. That way of working suits me very much. If you want to change something here you are not stopped, but you have to put your own energy into it. That creates freedom and responsibility, for me that is one of the biggest advantages of working at Ausnutria. And that's also how I prefer to learn: make plans, try, learn.
Nick: I can always leave Bart very free. Of course, sometimes I ask critical questions about certain choices, but I've never had to tell him to work harder to meet certain goals or deadlines. That's the kind of people we're looking for here. Bart wants to continuously improve. If he improves personally, we also improve as a company.
Bart: A good example of this is the Green Belt training I took through NextGen, and the practical assignment that came with it. There was too little capacity here in the factory, so we made sure that the cleaning time in a production line could be significantly reduced. That was very valuable, both in terms of the learning process and in ensuring higher production together and thus higher sales. For me, this is where the value of the collaboration between NextGen, the colleagues at Ausnutria and myself really lies.
Analyze and improve
Complex, high-impact projects
Complex, high-impact projects
Nick: NextGen's guidance during projects is very valuable. Together we provide a plan and set deadlines. NextGen ensures that there are clear agreements and that a project has a head and a tail. That reduces the risk for all parties. And in addition, there is good guidance. This project was ultimately completed entirely on schedule and has yielded more than we had expected.
Bart: That also gives good, new energy. I was actually going to stop at Ausnutria, but together we decided that I will now also go for the Black Belt. In the coming months, I am going to implement the same improvement process as I did before, but one that is a lot more complex. The responsibility is greater, but so is the impact. And the more responsibility I can grab, the more I like something.
Want to write your own Growth story?
Check out our open vacancies and who knows, maybe you'll soon be starting your own Next Level journey.